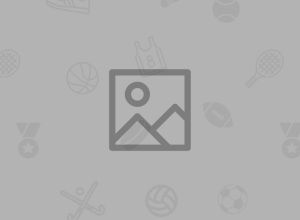
Understanding FRP Grating in the Electroplating Industry
In the realm of electroplating equipment factories, the demand for durable, corrosion-resistant materials has led to the widespread useof fiberglass reinforced plastic (FRP) grating. This versatile material excels in environments where exposure to harsh chemicals and moisture is routine. Its application in electroplating not only enhances the lifespan of the facilities but also promotes worker safety and operational efficiency.
Types of Fiberglass Grating for Electroplating Applications
Several types of fiberglass grating are tailored to meet the specific requirements of electroplating facilities. Here’s a closer look at the most common types:
- Standard Pultruded FRP Grating
Ideal for heavy-duty electroplating applications, pultruded FRP grating offers excellent load-bearing capabilities. This type of grating is known for its superior strength and durability, making it perfect for high-traffic areas and machinery bases. Its corrosion resistance is crucial for longevity in industrial electroplating settings. - Molded Fiberglass Grating
Molded fiberglass grating features a non-slip surface that provides stability in electroplating factories. This design is particularly beneficial in areas prone to spills, where safety is a priority. The uniform structure of molded grating minimizes the risk of accidents, contributing to a safer work environment. - Phenolic FRP Grating
Renowned for its fire resistance, phenolic FRP grating is becoming increasingly popular in electroplating equipment factories. This material meets stringent safety regulations, providing an additional layer of security in environments that handle flammable substances.
Key Specifications of GRP Grating in Electroplating
- GRP grating comes with specific features that enhance its functionality in electroplating environments:
- Corrosion Resistance: Essential for enduring the harsh chemicals often present in electroplating processes, fiberglass grating maintains its integrity over time.
- Anti-Slip Surface: Critical for ensuring safety in high-risk areas, this feature is designed to prevent slips and falls, particularly in wet conditions.
- Chemical Resistance: With the ability to withstand caustic substances, GRP grating offers a durable solution that minimizes maintenance costs in the long run.
Market Trends for FRP Grating in the Electroplating Sector
The application of FRP grating in electroplating is gaining momentum as industries prioritize sustainability and durability. More factories are turning to fiberglass solutions due to their lower maintenance requirements and extended lifespan compared to traditional materials. As environmental regulations tighten, the demand for corrosion-resistant fiberglass grating is expected to rise.
Applications of Fiberglass Grating in Electroplating Equipment
Fiberglass grating is employed in various applications within electroplating factories, including:
Walkways and Platforms: These installations provide safe, anti-slip surfaces that are easy to clean, ensuring compliance with health and safety standards.
Chemical Processing Areas: GRP grating is particularly suited for environments exposed to harsh chemicals, enhancing longevity while reducing replacement costs.
Machine Bases and Support Platforms: Heavy-duty FRP grating supports electroplating machinery, providing a stable foundation that can withstand heavy loads while resisting corrosion.
The Future of Fiberglass Grating in Electroplating
The application of FRP grating in electroplating will likely expand as industries increasingly recognize its benefits. The shift towards using more sustainable, durable materials aligns with broader trends in environmental responsibility. Companies are adopting fiberglass grating solutions to improve their operations while ensuring worker safety.
Moreover, products such as fiberglass stair railing and fiberglass floor tiles can enhance safety and accessibility in electroplating facilities, allowing for seamless integration with existing systems.
Conclusion
The application of FRP grating in electroplating equipment factories represents a critical advancement in materials used in the industry. With various options like pultruded, molded, and phenolic FRP grating, manufacturers can choose materials that meet their specific operational needs. By prioritizing safety, durability, and cost-effectiveness, the electroplating industry can benefit significantly from fiberglass grating solutions.
For more information on our range of fiberglass products, including molded fiberglass grating and pultruded grating, explore our product pages and see how these materials can transform your electroplating operations.
Leave a Comment